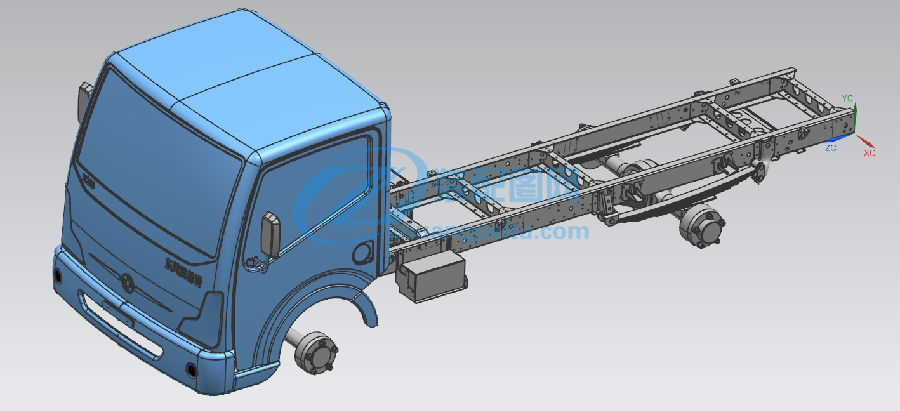

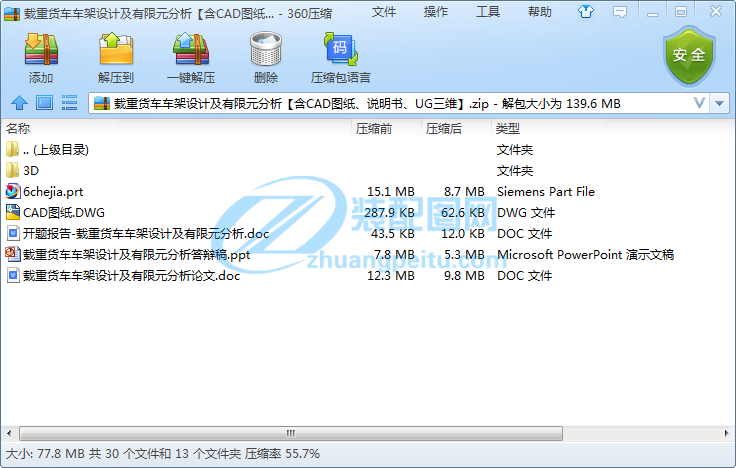
本科畢業(yè)設計(論文)開題報告
題 目 載重貨車車架設計及有限元分析
學 院 名 稱
專業(yè)班級
學生姓名
學 號
指 導 教 師
填表時間: 年 3 月 23日
填表說明
1.開題報告作為畢業(yè)設計(論文)答辯委員會對學生答辯資格審查的依據材料之一。
2.此報告應在指導教師指導下,由學生在畢業(yè)設計(論文)工作前期完成,經指導教師簽署意見、相關系主任審查后生效。
3.學生應按照學校統(tǒng)一設計的電子文檔標準格式,用A4紙打印。
4.參考文獻不少于8篇,其中應有適當的外文資料(一般不少于2篇)。
5.開題報告作為畢業(yè)設計(論文)資料,與畢業(yè)設計(論文)一同存檔。
設計(論文)
題目
載重貨車車架設計及有限元分析
設計(論文)
類型(劃“√”)
工程設計
應用研究
開發(fā)研究
基礎研究
其它
√
一、 本課題的研究目的和意義:
汽車車架作為重型載重汽車的基體,支承著發(fā)動機、離合器、變速器、轉向器、駕駛室、和貨箱等所有簧上質量的有關機件。并且使用條件十分惡劣受力狀況非常復雜,承受著來自車內外的各種力和力矩。同時載貨汽車行駛路況復雜車架在各種載荷作用下,將發(fā)生彎曲、偏心扭轉和整體扭轉等變形。因而車架應該有足夠的剛度、強度和足夠的可靠性與壽命。車架剛度不足會引起振動和噪聲,也是的汽車的舒適性和操作穩(wěn)定性下降。同時汽車的扭轉你剛度不宜過大,否則將使車架和懸架系統(tǒng)的載荷增大并使汽車車輪的的接地性變差。因此在車架設計時要充分考慮這些問題。傳統(tǒng)的車架設計方法很難綜合考慮汽車的復雜受力及變形情況,利有限元法正好能夠解決這一問題。同時利用有限元法進行結構模態(tài)分析,可以得到車架結構的動態(tài)特性。從設計上避免車架出現共振的現象。通過對車架結構的優(yōu)化設計,可以進一步降低車架的重量,在保證車架性能的前提下充分的節(jié)省材料,對降低車架的成本具有重要的意義。通過本次設計要熟練掌握載重汽車車架的設計流程及車架設計參數確定,同時更好的提高自己的二維三維作圖能力和有限元分析能力。建立車架結構有限元分析的規(guī)范化步驟,為將有限元技術應用于車架設計做好基礎性工作。通過運用有限元軟件對車架結構進行分析,可供車架設計提供參考。對所研究的車架進行結構的靜、動態(tài)特性分析,為車架的設計提供理論支持。最后對車架的設計做出優(yōu)化,盡量做到輕量化,提高車架的強度。同時盡可能的節(jié)省成本。
二、 本課題的主要研究內容(提綱)
1.了解熟悉目前國內各種重型貨車底盤種類,借鑒以往經驗結合目前國內路況設計車架總成結構。確定車架的總成參數,對車架縱梁參數,橫梁參數計算。對總體車架進行強度剛度等校核。符合設計標準。做出三維模擬圖。
2.對車架在各種典型工況下受到的載荷進行分析,根據受到的載荷信息結合ANSYS有限元分析軟件對車架進行靜態(tài)和模態(tài)分析。
3.根據有限元分析結果對車架進行適當的優(yōu)化。
三、 文獻綜述(國內外研究情況及其發(fā)展)
早期汽車所使用的車架,大多都是由籠狀的鋼骨梁柱所構成的,也就是在兩支平行的主梁上,以類似階梯的方式加上許多左右相連的副梁制造而成。車體建構在車架之上,至于車門、沙板、引擎蓋、行李廂蓋等鈑件,則是另外再包覆于車體之外,因此車體與車架其實是屬于兩個獨立的構造。這種設計的最大好處,在于輕量化與剛性得以同時兼顧。由于鋼骨設計的車架必須通過許多接點來連結主梁和副梁,加之籠狀構造也無法騰出較大的空間,因此除了制造上比較復雜、不利于大量生產。隨后單體結構的車架在車壇上成為主流,籠狀的鋼骨車架也逐漸改由這種將車體與車架合二為一的單體車架所取代,這種單體車架一般以“底盤”稱之。??
關于單體車架,簡單的說就是將引擎室、車廂以及行李廂三個空間合而為一,這樣的好處除了便于大量生產,模組化的運用也是其中主要的考慮。通過采取模組化生產的共用策略,車廠可以將同一具車架分別使用在數種不同的車款上,這樣也可節(jié)省不少研發(fā)經費。?
除了有利于共用,車體車架也可以通過材料的不同來發(fā)揮輕量化的特性,鋁合金是80年代末期相當熱門的一種工業(yè)材料,雖然重量比鐵輕,但是強度卻較差,因此如果要用鋁合金制成單體車架,雖然在重量上比起鐵制車架更占優(yōu)勢,但是強度卻無法達到和鐵制車架同樣的水準。除非增加更多的鋁合金材料,利用更多的用量來彌補強度上的不足。不過這樣一來,重量必然會相對增加,而原本出于輕量化考量而采用鋁合金材料的動機,當然也就失去了意義。也正因為這個原因,鋁合金車架在車壇上并未成為主流,少數高性能跑車或是使用了強度更高的碳纖維,或是用碳纖維結合蜂巢狀夾層鋁合金的復合材料取代了鋁合金。但是要用碳纖維制成單體車架,在制作上相當復雜且費時,成本也相對更高,所以至今仍無法普及到一般市售車上,而僅有少數售價高昂的跑車使用,這些是不可能用在載重貨車上的。?盡管鋁合金車架鮮有車廠使用,不過用鋼鐵車架搭配鋁合金鈑件的方式,近年來卻受到不少車廠的重視,這樣的結構不僅可以保留車架本身的強度,同時也可以通過鈑件的鋁合金化來取得輕量化效果,在研發(fā)成本上自然也不像碳纖維制的單體車架那樣昂貴。?
載貨汽車行駛路況復雜車架在各種載荷作用下,將發(fā)生彎曲、偏心扭轉和整體扭轉等變形。目前國內商用車車架設計開始從原有的單純經驗設計進入優(yōu)化設計階段,主要特點是以有限元計算分析等手段輔助設計,在零件試制之前對產品就有了初步判斷,可以提前解決相當數量的設計問題,但目前有限元分析還只局限在強度計算方面,壽命計算做的較少再有一點就是目前國內車架的開發(fā)很少經過臺架強度和壽命試驗,而目前國內各汽車生產廠車架臺架試驗所需的硬件應該沒有問題,主要問題缺少參數輸入方面的積累。另外,由于目前國內還無法杜絕超載現象的存在,所以我們的車架設計偏于保守。相反,國外商用車車架開發(fā)過程中有限元分析應用比較廣泛,而且臺架試驗應用也被大量采用,有比較成熟的車架臺架試驗經驗,比如奧地利斯太爾公司的臺架試驗現在已經非常成熟,車架總成在通過斯太爾的 250 小時脈沖臺架試驗后只需要進行 300 小時的場地試驗,檢驗連接件的可靠性即可,通過這兩項試驗,車架的使用壽命可到 100 萬公里,目前 BENZ,MAN 等公司仍利用斯太爾的試驗臺進行車架臺架試驗,它們的車架如果不經過脈沖試驗,整車不投產。從材料的使用情況看,目前在節(jié)油、輕量化的壓力下,國內外重型商用車車架普遍采用了高強度鋼板,2S\500Mpa 的鋼板已經廣泛應用 從成型工藝方面看,傳統(tǒng)的縱梁制造工藝采用大型沖壓設備及大型模具沖壓成型,一次性生產準備投入大,周期長,柔性化差,精度不高,很難適應產品和市場的變化。而且,隨著縱梁所用材料強度等級的不斷提高,采用傳統(tǒng)制造工藝所需的沖壓設備會越來越大,對材料的成型性能要求也高,很難適應發(fā)展的需要。所以目前普遍采用的是縱梁滾壓成型制造工藝,其特點是:柔性化好,精度高,一次性生產準備投入小。
歐美從90年代開始逐漸提高了撞擊事故的安全防護標準,這也是凸現出車架剛性重要的另一原因。許多車廠為了在撞擊事故發(fā)生時能夠確保車內乘員的安全,惟有針對車架以及車體進行全面強化,這也使得除了車架以外的強度有所改善,包括鈑件厚度的改變以及各種輔助梁的增設也成為各廠慣用的手法。不過在這樣的情況下,伴隨而來的是車重相對增加,這也正是歐美日許多市售車的重量比起10年前、20年前增加不少的主要原因。?關于剛性的確保,大多數車廠在新車的設計階段,都是利用電腦計算出車架的剛性需求,并以此作為設計依據。有些車廠在用電腦完成設計雛形后,還會再由專業(yè)的試車人員進行實際測試。
中國第一汽車集團凌源汽車制造有限公司汽車車架U型槽合數控沖孔生產線競標成功。?汽車車架U型槽合數控沖孔生產線是我公司繼兩年前成功設計制造了合肥江淮汽車廠汽車縱梁數控平板沖孔生產線的基礎上,在汽車縱梁數控沖孔方面的又一標志性成果,填補了國內設計制造汽車車架U型槽合數控沖孔生產線的空白。汽車車架U型槽合數控沖孔生產線的設計制造成功,在汽車制造行業(yè)具有劃時代的意義,標志著中國在汽車車架數控沖孔加工的生產設備方面達到了國際先進水平,降低了汽車制造行業(yè)購置汽車車架數控沖孔生產線的巨大費用,積極推動了中國汽車制造業(yè)的飛速發(fā)展,為中國汽車制造業(yè)早日與國際接軌奠定了基礎。?
目前我國的車架企業(yè)基本擁有剪切、沖壓、焊接、鉚接、油漆、機加工六大工藝能力和完善的檢測手段、研究設計中心,具有16噸至3000噸的冷沖壓能力,具備了開發(fā)、設計、生產各種類型車架。
四、 擬解決的關鍵問題
1、運用大學期間所學的專業(yè)課程知識、理論和畢業(yè)實習中學到的實踐知識,設計一款重型貨車車架總成,確定各方面詳細參數,完善汽車車架,選擇合適的車架材料和加工工藝,保證車架的剛度和強度。按照行業(yè)標準對車架進行校核。做出三維模擬圖。
2、利用ANSYS有限元分析軟件對車架進行靜態(tài)和模態(tài)分析,并根據分析結果對車架進行優(yōu)化。
五、 研究思路和方法
1、首先采用類比的方法,查閱目前國內外市場上載重貨車的車架類型及參數,分析消化,對已有的某一款車架作出改進,重新確定其總成及參數。對車架的剛度和強度進行校核。
2、分析貨車的各種典型行駛工況,確定其所受到的各種動態(tài)載荷形式,利用ANSYS有限元分析軟件根據其所受載荷進行靜態(tài)和模態(tài)分析,確定其強度及使用可靠性。
3、根據分析結果對車架做出優(yōu)化改進。
六、 本課題的進度安排
第?3-4周? 查閱資料確定課題,填寫開題報告。查找翻譯英語譯文。??
第?5-7?周??車架結構設計,確定車架總成,車架縱梁、橫梁確定,強度校核。
第?8-9?周??車架二維圖紙,三維模型建立。
?第10-13周??對車架進行有限元分析并作出優(yōu)化。
第14-15周??寫畢業(yè)論文,做畢業(yè)答辯。
七、 參考文獻
[1]?陳家瑞.?汽車構造. 北京:人民交通出版社,2008,9.161~168
[2]?余志生.?汽車理論.?北京: 機械工業(yè)出版社,?2000,10.96~103
[3] 尹輝俊,韋志林,沈光烈. 貨車車架有限元分析[J]. 機械設計 2005.11:26~38
[4] 肖柳勝,劉健,袁艷艷,馬曉偉,吳漢川. 基于多工況的的重載壓裂車架靜動態(tài)強度分析[J]. 西華大學學報(自然科學版), 2015,2.
[5] Dr.R.Rajappan,M.Vivekanandhan. Design of Improvement for Heavy Dump Truck Frame without Assistant Frame. 2010 International Conference on Computational Intelligence and Vehicular System,2010,10
[6] 胡亞莊,黃天澤.載重汽車與掛車的車架[M].北京:人民交通出版社,1964.
[7] Frederic Dieu,Structural Optimization of A Vehicle Using Finite Element
Techniques[J],SAE Paper 885135;
[8] Tushar M. Patel ,Dr. M. G. Bhatt and Harshad K. Patel . Analysis and validation of Eicher 11.10 chassis frame using Ansys International Journal of Em erging Trends & Technology in Com puter Science (IJETTCS)[J] Volume 2, Issue 2, March – April 2013
[9] Dr.R.Rajappan, M.Vivekanandhan. Static and model analysis of chassis by using FEA. Proceedings of the “National Conference on Emerging Trends In Mechanical Engineering 2k13
指導教師意見
指導教師(簽名):
年 月 日
所在系(所)意見
負責人(簽章):
年 月 日
載重貨車車架設計及有限元分析,學生:,選題背景,車架是汽車的裝配基體和承載基體,支承連接汽車的各總成或零部件,下面與輪轂板簧連接。車架不僅承擔質量載荷,還承受汽車行駛過程中產生的各種力和力矩。因此在設計過程中,保證車架足夠的強度和剛度是很有必要的。,,車架的設計方法目前主要是經驗設計法,同時結合有限元分析法對其進行靜力分析、模態(tài)分析和疲勞分析。 本文基于福田奧鈴CTX貨車進行車架設計,并對其進行靜力分析和模態(tài)分析,,,主要內容,車架類型選擇及總成參數設計 建立車架的三維模型 靜力分析 模態(tài)分析,車架類型選擇及總成參數設計,車架的結構形式可以分為邊梁式、中梁式和綜合式。邊梁式車架由兩根縱梁和若干根橫梁組成,其優(yōu)點是彎曲剛度較大,便于安裝,易于改裝,因此被廣泛應用。,,中梁式車架只有一根位于中央而貫穿汽車全長的縱梁 ,優(yōu)點是有較好的抗扭轉剛度和較大的前輪轉向角,但是制造工藝復雜,精度要求高,故目前應用較少。,,綜合式車架是由邊梁式和中梁式車架聯(lián)合構成的。此種結構在轎車上使用較多。 綜合考慮本次設計采用邊梁式車架??v梁上、下表面為平直,斷面呈槽形。,車架總成參數的確定,本次設計車架的長度為整車的長度減去保險杠最前端到車架最前端的距離確定總長為 8400mm,車架前懸為 1150mm,軸距為4700mm,車架后懸為 2550mm。車架寬度根據我國(汽132-59載重汽車車架寬度標準)規(guī)定“車架寬度標準為865 ±5毫米”。根據汽車設計取車架寬860mm。 本次設計中共采用六根橫梁,其中第二根橫梁用來支撐發(fā)動機采用元寶梁,其他梁均采用斷面為槽型的梁。橫梁與縱梁之間的連接方式采用鉚接加焊接的方式。橫梁鉚接在直角鋼上,直角鋼通過螺栓連接在縱梁腹板上。,建立車架的三維實體模型,本文用solidworks軟件建立了三維實體模型。,建立車架的有限元模型,在solidworks軟件中將車架的三維模型完成之后,將模型轉化為Workbench 軟件所識別的*.x-t格式 .定義材料屬性,劃分網格,生成有限元模型。,加載方式,車架在靜止時只承受懸架以上部分的載荷,包括駕駛室,發(fā)動機變速箱以及滿載油箱等。這些載荷分布在車架結構上,有的做均布載荷處理,平均分配到縱梁上;有的做集中力處理,作用在相應的節(jié)點上。,,滿載彎曲工況,滿載彎曲工況是模擬汽車在滿載狀態(tài)下,四輪著地在良好路面上勻速行駛時車架對其所承受的重量的響應。,,滿載彎曲工況內部應力云圖,滿載彎曲工況下位移云圖,30%超載彎曲工況,與滿載相比,后車架貨箱位置多施加30%負載 ,把貨箱載重增加30%,是車架的一種極限工況。,30%超載位移云圖,30%超載 應力云圖 最大應力出現在后輪后支撐處,,滿載扭轉工況,扭轉工況主要是模擬汽車一側輪胎駛入凹坑或是遇到凸起障礙物時,車架發(fā)生最為嚴重扭曲,此時車架受到的應力及變形情況最為惡劣。給右前輪強制施加一個10mm的位移,其余三個輪按固定位移處理。,,滿載扭轉工況下的位移云圖,滿載扭轉工況下應力云圖,滿載制動工況,模擬車輛遇到緊急情況進行制動時的情況,本文研究的是滿載緊急制動工況,制動工況考慮前后車輪完全抱死的情況下,取附著系數φ=0.7,汽車制動時的最大減速度為0.7m/s。,,滿載制動工況下位移云圖,滿載制動應力云圖,滿載轉彎工況,汽車在行駛過程中,有時會遇到急轉彎的情況,因此離心力的作用,車架將受到側向加速度。按緊急右轉的極限狀態(tài)。轉彎狀況下車速按20km/h計算,轉彎半徑按10m計算。 根據a=V2/R 計算出側向加速度2.5m/s2 。,,滿載轉彎應力云圖,滿載轉彎工況下位移云圖,分析小結,,通過對車架四種典型工況靜態(tài)分析可以看出,貨車在除扭轉工況外,其余各種工況下,安全系數均大于1,就算在超載30%以后,車架的安全系數仍然大于1.因此此時可以考慮減薄壁厚來實現車架的輕量化,只有在扭轉工況時車架與懸架連接處的內部應力超過材料的屈服強度,因此可以通過強度更高強度的材料來替換懸架與車架連接處的材料,達到更安全的目的。 同時還可以通過增大橫梁上的圓孔直徑來減少材料用量,已達到輕量化的目的。從經濟方面考慮,也可以換用價格更低廉的材料。,模態(tài)分析,在汽車行駛時,所受的載荷大部分為動載荷。尤其是凹凸不平的路面,它對車輛產生隨機激勵。再加上發(fā)動機轉動產生激振頻率。如果這幾種激振頻率與車架的固有頻率相同或是接近,產生共振。因此我們有必要通過模態(tài)分析可以得到車架的固有頻率和主要振型。避免共振的發(fā)生。,,,車架外部激勵分析,根據發(fā)動機激勵計算公式F=2nz/60τ( z 為發(fā)動機缸數; τ 為發(fā)動機沖程數)和廠家提供的發(fā)動機數據,貨車發(fā)動機怠速激振頻率為20~26Hz,最大功率激振頻率為86Hz,最大轉矩激振頻率為43Hz。 路面對車架激勵的頻率,不僅與路面狀況有關,還與車速有關。根據路面激勵頻率計算公式f=Vmax/3.6Lmax (Lmax為路面不平度波長 )重型貨車主要行駛的3種路面產生的激振頻率,模態(tài)分析與激勵總結,根據上述分析可知,發(fā)動機怠速時發(fā)出的激振頻率為20~26Hz,遠低于車架的一階模態(tài)頻率,不會與車架發(fā)生共振。發(fā)動機最大功率轉速時的激振頻率為86Hz,介于四階模態(tài)頻率和五階模態(tài)頻率之間,也不會與車架發(fā)生共振,發(fā)動機最大轉矩轉速時的激振頻率為43Hz,與車架三階模態(tài)頻率41.53Hz接近,車架可能發(fā)生共振。此時可以通過增加配重或是更改橫梁位置等方法更改車架的三階模態(tài)頻率,防止車架發(fā)生共振。車架的一階模態(tài)頻率均大于3種路況所產生的路面激勵。因此貨車在行駛過程中,不會因路面的激勵而產生車架共振。,謝謝各位答辯老師的評審,請各位老師指正!,載重貨車車架設計及有限元分析
摘要
汽車車架是整個汽車的基體,是汽車設計中一個重要的環(huán)節(jié)。車架支撐著發(fā)動機離合器、變速器、轉向器、非承載式車身和貨箱等所有簧上質量的重要機件,承受著傳給它的各種力和力矩。因此,車架必須要有足夠的彎曲剛度,也要有足夠的強度,以保證其有足夠的可靠性與壽命。同時,隨著現在汽車的發(fā)展,載重貨車的乘坐舒適性,操控性能也在不斷提高,因此車架的設計還應同時兼顧舒適性和操控性。
本文以商用載重貨車為研究目標,結合貨車的各項參數,對車架進行設計。確定了車架總成以及縱梁橫梁的各項參數。運用solidworks軟件做出了車架的三維模型圖。同時利用ANSYS WORKBENCH有限元分析軟件對車架的四種典型工況做出靜力分析,得到各種工況下的變形情況和應力分布情況,同時對車架進行了模態(tài)分析。最后根據分析結果對車架做出優(yōu)化建議。
關鍵詞: 載重貨車;車架;結構設計;有限元分析
ABSTRACT
The vehicle frame is?the base of?the car,?is one of the most important parts?in the automobile design.?Frame supports the engine clutch, transmission, steering gear, non bearing body and the container all spring quality the important parts, bear and pass it on to all kinds of force and moment.?Therefore, the frame must have enough bending stiffness, also want to have enough strength, to ensure sufficient reliability and life.?At the same time, with now the development of automobile and truck ride comfort, handling performance also continues to increase, so design of the frame should also combine comfort and handling.
In this paper, the commercial truck as the research objective, combined with the parameters of the truck, the frame design. Frame assembly and the longitudinal beam parameters were determined. The 3D model chart of the frame was made by SolidWorks software.. At the same time, the finite element analysis software ANSYS Workbench of the frame of four kinds of typical working conditions to make static analysis, obtained under various conditions of deformation and stress distribution, and the modal analysis of the frame. Finally, according to the results of the analysis of the frame to make optimization recommendations.
Keywords: Truck;?frame;structure design;? finite element analysis
目錄
摘要 I
ABSTRACT II
1 緒論 1
1.1車架總成概述 1
1.2國內外研究情況及其發(fā)展 2
2 車架總成設計 6
2.1參考車型及其參數 6
2.2車架類型的選擇 6
2.3車架設計的技術要求 11
2.4車架的輕量化 13
2.5車架的參數設計 13
3 車架的有限元靜力學分析 19
3.1車架幾何模型的建立 19
3.2車架有限元模型的建立 19
3.3車架的靜力學分析 21
3.4 基于靜力分析的車架輕量化 35
4 車架的模態(tài)分析 37
4.1車架模態(tài)分析的基本理論 37
4.2車架有限元模態(tài)分析結果 39
4.3車架外部激勵分析 43
5 總結與展望 46
5.1總結 46
5.2工作展望 46
參考文獻 48
致謝 50
附錄 51
68
1 緒 論
1.1車架總成概述
汽車車架是整個汽車的基體,是將汽車的主要總成和部件連接成汽車整體的金屬構架,對于這種金屬構架式車架,生產廠家在生產設計時應考慮結構合理,生產工藝規(guī)范,要采取一切切實可行的措施消除工藝缺陷,保證它在各種復雜的受力情況下不至于被破壞。
車架作為汽車的承載基體,為貨車、中型及以下的客車、中高級和高級轎車所采用,支撐著發(fā)動機離合器、變速器、轉向器、非承載式車身和貨箱等所有簧上質量的有關機件,承受著傳給它的各種力和力矩。為此,車架應有足夠的彎曲剛度,以使裝在其上的有關機構之間的相對位置在汽車行駛過程中保持不變并使車身的變形最??;車架也應有足夠的強度,以保證其有足夠的可靠性與壽命,縱梁等主要零件在使用期內不應有嚴重變形和開裂。車架剛度不足會引起振動和噪聲,也使汽車的乘坐舒適性、操縱穩(wěn)定性及某些機件的可靠性下降。
本文只是敘述非承載式車身結構形式中單獨的車架系統(tǒng)。承載式汽車,前、后懸架裝置,發(fā)動機及變速器等傳動系部件施加的作用力均由車架承受,所以,車架總成的剛性、強度及振動特性等幾乎完全決定了車輛整體的強度、剛度和振動特性。設計時在確保車架總成性能的同時,還應對車架性能和匹配性進行認真的研究。車架結構很多都是用電弧焊焊接而成,容易產生焊接變形。在設計方面對精度有要求的部位不得出現集中焊接,或者從部件結構方面下工夫,盡量確保各個總成的精度。另外,與其他焊接方法相對比,采用電弧焊的話,后端部容易出現比較大的缺口,出現應力集中現象。所以,應對接頭位置和焊接端部進行處理[1]。
車架受力狀態(tài)極為復雜。汽車靜止時,它在懸架系統(tǒng)的支撐下,承受著汽車各部件及載荷的重力,引起縱梁的彎曲和偏心扭轉(局部扭轉)。如汽車所處的路面不平,車架還將呈現整體扭轉。汽車行駛時,載荷和汽車各部件的自身質量及其工作載荷(如驅動力、制動力和轉向力等)將使車架各部件承受著不同方向、不同程度和隨機變化的動載荷,車架的彎曲、偏心扭轉和整體扭轉將更嚴重,同時還會出現側彎、菱形傾向,以及各種彎曲和扭轉振動。同時,有些裝置件還可能使車架產生較大的裝置載荷[2]。
隨著計算機技術的發(fā)展,在產品開發(fā)階段,對車架靜應力、剛度、振動模態(tài)以至動應力和碰撞安全等已可進行有限元分析,對其輕量化、使用壽命,以及振動和噪聲特性也可以做出初步判斷,為縮短產品開發(fā)周期創(chuàng)造了有利條件。
1.2國內外研究情況及其發(fā)展
早期汽車所使用的車架,大多都是由籠狀的鋼骨梁柱所構成的,也就是在兩支平行的主梁上,以類似階梯的方式加上許多左右相連的副梁制造而成。車體建構在車架之上,至于車門、沙板、引擎蓋、行李廂蓋等鈑件,則是另外再包覆于車體之外,因此車體與車架其實是屬于兩個獨立的構造。這種設計的最大好處,在于輕量化與剛性得以同時兼顧。由于鋼骨設計的車架必須通過許多接點來連結主梁和副梁,加之籠狀構造也無法騰出較大的空間,因此除了制造上比較復雜、不利于大量生產。隨后單體結構的車架在車壇上成為主流,籠狀的鋼骨車架也逐漸改由這種將車體與車架合二為一的單體車架所取代,這種單體車架一般以“底盤”稱之[3]。??
關于單體車架,簡單的說就是將引擎室、車廂以及行李廂三個空間合而為一,這樣的好處除了便于大量生產,模組化的運用也是其中主要的考慮。通過采取模組化生產的共用策略,車廠可以將同一具車架分別使用在數種不同的車款上,這樣也可節(jié)省不少研發(fā)經費。?
除了有利于共用,車體車架也可以通過材料的不同來發(fā)揮輕量化的特性,鋁合金是80年代末期相當熱門的一種工業(yè)材料,雖然重量比鐵輕,但是強度卻較差,因此如果要用鋁合金制成單體車架,雖然在重量上比起鐵制車架更占優(yōu)勢,但是強度卻無法達到和鐵制車架同樣的水準。除非增加更多的鋁合金材料,利用更多的用量來彌補強度上的不足。不過這樣一來,重量必然會相對增加,而原本出于輕量化考量而采用鋁合金材料的動機,當然也就失去了意義[4]。也正因為這個原因,鋁合金車架在車壇上并未成為主流,少數高性能跑車或是使用了強度更高的碳纖維,或是用碳纖維結合蜂巢狀夾層鋁合金的復合材料取代了鋁合金。但是要用碳纖維制成單體車架,在制作上相當復雜且費時,成本也相對更高,所以至今仍無法普及到一般市售車上,而僅有少數售價高昂的跑車使用,這些是不可能用在載重貨車上的。?盡管鋁合金車架鮮有車廠使用,不過用鋼鐵車架搭配鋁合金鈑件的方式,近年來卻受到不少車廠的重視,這樣的結構不僅可以保留車架本身的強度,同時也可以通過鈑件的鋁合金化來取得輕量化效果,在研發(fā)成本上自然也不像碳纖維制的單體車架那樣昂貴。?
載貨汽車行駛路況復雜車架在各種載荷作用下,將發(fā)生彎曲、偏心扭轉和整體扭轉等變形。目前國內商用車車架設計開始從原有的單純經驗設計進入優(yōu)化設計階段,主要特點是以有限元計算分析等手段輔助設計,在零件試制之前對產品就有了初步判斷,可以提前解決相當數量的設計問題,但目前有限元分析還只局限在強度計算方面,壽命計算做的較少再有一點就是目前國內車架的開發(fā)很少經過臺架強度和壽命試驗,而目前國內各汽車生產廠車架臺架試驗所需的硬件應該沒有問題,主要問題缺少參數輸入方面的積累[5]。另外,由于目前國內還無法杜絕超載現象的存在,所以我們的車架設計偏于保守。相反,國外商用車車架開發(fā)過程中有限元分析應用比較廣泛,而且臺架試驗應用也被大量采用,有比較成熟的車架臺架試驗經驗,比如奧地利斯太爾公司的臺架試驗現在已經非常成熟,車架總成在通過斯太爾的 250 小時脈沖臺架試驗后只需要進行 300 小時的場地試驗,檢驗連接件的可靠性即可,通過這兩項試驗,車架的使用壽命可到 100 萬公里,目前 BENZ,MAN 等公司仍利用斯太爾的試驗臺進行車架臺架試驗,它們的車架如果不經過脈沖試驗,整車不投產[6]。從材料的使用情況看,目前在節(jié)油、輕量化的壓力下,國內外重型商用車車架普遍采用了高強度鋼板,500Mpa/S2 的鋼板已經廣泛應用 從成型工藝方面看,傳統(tǒng)的縱梁制造工藝采用大型沖壓設備及大型模具沖壓成型,一次性生產準備投入大,周期長,柔性化差,精度不高,很難適應產品和市場的變化。而且,隨著縱梁所用材料強度等級的不斷提高,采用傳統(tǒng)制造工藝所需的沖壓設備會越來越大,對材料的成型性能要求也高,很難適應發(fā)展的需要。所以目前普遍采用的是縱梁滾壓成型制造工藝,其特點是:柔性化好,精度高,一次性生產準備投入小[7]。
歐美從90年代開始逐漸提高了撞擊事故的安全防護標準,這也是凸現出車架剛性重要的另一原因[8]。許多車廠為了在撞擊事故發(fā)生時能夠確保車內乘員的安全,惟有針對車架以及車體進行全面強化,這也使得除了車架以外的強度有所改善,包括鈑件厚度的改變以及各種輔助梁的增設也成為各廠慣用的手法。不過在這樣的情況下,伴隨而來的是車重相對增加,這也正是歐美日許多市售車的重量比起10年前、20年前增加不少的主要原因。?關于剛性的確保,大多數車廠在新車的設計階段,都是利用電腦計算出車架的剛性需求,并以此作為設計依據。有些車廠在用電腦完成設計雛形后,還會再由專業(yè)的試車人員進行實際測試。
中國第一汽車集團凌源汽車制造有限公司汽車車架U型槽合數控沖孔生產線競標成功。?汽車車架U型槽合數控沖孔生產線是我公司繼兩年前成功設計制造了合肥江淮汽車廠汽車縱梁數控平板沖孔生產線的基礎上,在汽車縱梁數控沖孔方面的又一標志性成果,填補了國內設計制造汽車車架U型槽合數控沖孔生產線的空白。汽車車架U型槽合數控沖孔生產線的設計制造成功,在汽車制造行業(yè)具有劃時代的意義,標志著中國在汽車車架數控沖孔加工的生產設備方面達到了國際先進水平,降低了汽車制造行業(yè)購置汽車車架數控沖孔生產線的巨大費用,積極推動了中國汽車制造業(yè)的飛速發(fā)展,為中國汽車制造業(yè)早日與國際接軌奠定了基礎。?
目前我國的車架企業(yè)基本擁有剪切、沖壓、焊接、鉚接、油漆、機加工六大工藝能力和完善的檢測手段、研究設計中心,具有16噸至3000噸的冷沖壓能力,具備了開發(fā)、設計、生產各種類型車架。
2 車架總成設計
2.1參考車型及其參數
參考車型:奧鈴CTX BJ1151VKPFG-S
詳細參數:
發(fā)動機型號:康明斯ISF3.8S3154 發(fā)動機功率:115kw
最大扭矩:500N.M 最大馬力:154馬力
發(fā)動機排量:3760 ML 發(fā)動機類型:柴油發(fā)動機
外形尺寸(長×寬×高):8445×2270×2500 mm
貨箱欄板內尺寸:6200×2100×550 mm
總質量:14785 Kg 整備質量:4600Kg
額定載質量:9990 Kg 接近角/離去角:23/16
前懸/后懸:1195/2250mm 軸距:4700 mm
軸荷:5280/9505N 最高車速:95 km/h
前輪距:1710 mm 后輪距:1680 mm
底盤型號:BJ1151VKPFG-S 軸數:2
彈簧片數:8/10+10
輪胎數:6 輪胎規(guī)格:8.25-20
2.2車架類型的選擇
車架的結構形式可以分為邊梁式、中梁式(或稱脊骨式)和綜合式。而在有些客車和轎車上車身和車架制成一體,這樣的車身稱為“半承載式車身”,有的被加強了車身則能完全起到車架的作用,這樣的車身稱為“承載式車身”,不另設車架。隨著節(jié)能技術的發(fā)展,為了減輕自重,越來越多的轎車都采用了承載式車身[9]。下邊先分別列舉下各車架的特點。
(1)邊梁式車架的構造
這種車架由兩根縱梁及連接兩根縱梁的若干根橫梁組成,用鉚接和焊接的方法將縱橫梁連接成堅固的剛性構架。縱梁通常用低合金鋼板沖壓而成,斷面一般為槽型,z星或箱型斷面。橫梁用來連接縱梁,保證車架的抗扭剛度和承載能力,而且還用來支撐汽車上的主要部件。 邊梁式車架能給改裝變型車提供一個方便的安裝骨架,因而在載重汽車和特種車上得到廣泛用。其彎曲剛度較大,而當承受扭矩時,各部分同時產生彎曲和扭轉。其優(yōu)點是便于安裝車身、車箱和布置其他總成,易于汽車的改裝和變形,因此被廣泛地用在載貨汽車、越野汽車、特種汽車和用貨車底盤改裝而成的大客車上。在中、輕型客車上也有所采用,轎車則較少采用。
用于載貨汽車的邊梁式車架(圖2.1),由兩根相互平行但開口朝內、沖壓制成的槽型縱梁及一些沖壓制成的開口槽型橫梁組合而成。通常,縱梁的上表面沿全長不變或局部降低,而兩端的下表面則可以根據應力情況相應地縮小。車架寬度多為全長等寬。
邊梁式車架
圖 2.1 邊梁式車架
(2)X梁型車架
X型車架(圖2.2)是邊梁式車架的改進,這種車架由兩根縱梁及X型橫梁組成,實際上是邊梁式車架的改進,有一定的抗扭剛度,X橫梁能將扭矩轉變?yōu)閺澗兀瑢Χ潭鴮挼能嚰?,這種效果最明顯。車架中部為位于汽車縱向對稱平面上的一根矩形斷面的空心脊梁,其前后端焊以叉形梁。前端的叉形梁用于支撐動力、傳動總成,而后端則用于安裝后橋。傳動軸經中部管梁通向后方。中部管梁的扭轉剛度大。前后叉形邊梁由一些橫梁相連,后者還用于加強前、后懸架的支撐。管梁部分位于后座乘客的腳下位置且在車寬的中間,因此不妨礙在其兩側的車身地板的降低,但地板中間會有較大的縱向鼓包。門檻的寬度不大,雖然從被動安全性考慮,要求門檻有足夠的強度和剛度。轎車要是使用邊梁式車架,為了降低地板高度,可局部地減少縱梁的斷面高度并相應地加大其寬度,但這使縱梁的制造工藝復雜化且其車身地板仍比采用其他車架時為高,當然地板上的傳動軸通道鼓包也就不大了。所以X型車架較多使用于轎車。
圖 2.2 X梁式車架
(3)周邊式車架
周邊式車架,這種車架是從邊梁式車架派生出來的,前后兩端縱梁變窄,中部縱梁加寬,前端寬度取決于前輪最大轉角,后端寬度取決于后輪距,中部寬度取決于車身門檻梁的內壁寬,前部和中部以及后部和中部的連接處用緩沖臂或抗扭盒相連,具有一定的彈性,能緩和不平路面的沖擊。其結構形狀容許緩沖臂有一定的彈性變形,可以吸收來自不平路面的沖擊和降低車內噪聲。此外,車架中部加寬既有利于提高汽車的橫向穩(wěn)定性,又可以減短了車架縱梁外側裝置件的懸伸長度。在前后縱梁處向上彎曲以讓出前后獨立懸架或非斷開式后橋的運動空間。采用這種車架時車身地板上的傳動軸通道所形成的鼓包不大,但門檻較寬。這種車架結構復雜,一般在中、高級轎車上采用。
(4)中梁式車架(脊骨式車架)
其結構只有一根位于中央而貫穿汽車全長的縱梁,亦稱為脊骨式車架(圖2.3)。中梁的斷面可做成管形、槽形或箱形。中梁的前端做成伸出支架,用以固定發(fā)動機,而主減速器殼通常固定在中梁的尾端,形成斷開式后驅動橋。中梁上的懸伸托架用以支承汽車車身和安裝其它機件。若中梁是管形的,傳動軸可在管內穿過。優(yōu)點是有較好的抗扭轉剛度和較大的前輪轉向角,在結構上容許車乾有較大的跳動空間,便于裝用獨立懸架,從而提高了汽車的越野性;與同噸位的載貨汽車相比,其車架輕,整車質量小,同時質心也較低,故行駛穩(wěn)定性好;車架的強度和剛度較大;脊梁還能起封閉傳動軸的防塵罩作用。缺點是制造工藝復雜,精度要求高,總成安裝困難,維護修理也不方便,故目前應用較少。
(5)綜合式車架
綜合式車架(圖2.4)是由邊梁式和中梁式車架聯(lián)合構成的。車架的前段或后段是邊梁式結構,用以安裝發(fā)動機或后驅動橋。而車架的另一段是中梁式結構的支架可以固定車身。傳動軸從中梁的中間穿過,使之密封防塵。其中部的抗扭剛度合適,但中部地板凸包較大,且制造工藝較復雜。此種
圖 2.3中梁式車架
結構一般在轎車上使用。車架承受著全車的大部分重量,在汽車行駛時,它承受來自裝配在其上的各部件傳來的力及其相應的力矩的作用。當汽車行駛在崎嶇不平的道路上時,車架在載荷作用下會產生扭轉變形,使安裝在其上的各部件相互位置發(fā)生變化。當車輪受到沖擊時,車架也會相應受到沖擊載荷。因而要求車架具有足夠的強度,合適的剛度,同時盡量減輕重量。在良好路面行駛的汽車,車架應布置得離地面近一些,使汽車重心降低,有利于汽車穩(wěn)定行駛,車架的形狀尺寸還應保證前輪轉向要求的空間[10]。
由于設計的是載貨汽車車架,根據其特點選用邊梁式車架??v梁上、下表面為平直,斷面呈槽形,其結構簡單,工作可靠,不僅能降低工人工作強度,而且其造價低廉,有良好的經濟性,將廣泛地用于各種載貨汽車、客車上。
圖 2.4 綜合式車架
2.3車架設計的技術要求
為了使車架符合上述功用,通常對設計的車架必須要有足夠的強度。以保證在各種復雜受力的使用情況下車架不受破壞。要求有足夠的疲勞強度,保證在汽車大修里程內,車架不致有嚴重的疲勞損傷。
縱梁受力極為復雜,設計時不僅應注意各種應力,改善其分布情況,還應該注意使各種應力峰值不出現在同一部位上。例如,縱梁中部彎曲應力較大,則應注意降低其扭轉應力,減少應力集中并避免失穩(wěn)。而在前、后端,則應著重控制懸架系統(tǒng)引起的局部扭轉[11]。
提高縱梁強度常用的措施如下:
(1)提高彎曲強度
選定較大的斷面尺寸和合理的斷面形狀(槽形梁斷面高寬比一般為3:1左右);
(2)提高局部扭轉剛度
注意偏心載荷的布置,使相近的幾個偏心載荷盡量接近縱梁斷面的彎曲中心,并使合成量較?。?
在偏心載荷較大處設置橫梁,并根據載荷大小及分散情況確定連接強度和寬度;
將懸置點分布在橫梁的彎曲中心上;當偏心載荷較大并偏離橫梁較遠處時候,可以采用K形梁,或者將該段縱梁形成封閉斷面;偏心載荷較大且比較分散時候,應該采用封閉斷面梁,橫梁間距也應縮小;
選用較大的斷面;
限制制造扭曲度,減少裝配預應力。
(3)提高整體扭轉強度
不使縱梁斷面過大;
翼緣連接的橫梁不宜相距太近。
(4)減少應力集中及疲勞敏感
盡可能減少翼緣上的孔(特別是高應力區(qū)),嚴禁在翼緣上布置大孔;
注意外形的變化,避免出現波紋區(qū)或者受嚴重變?。?
注意加強端部的形狀和連接,避免剛度突變;
避免在槽形梁的翼緣邊緣處施焊,尤其畏忌短焊縫和“點”焊。
(5)減少失穩(wěn)
受壓翼緣寬度和厚度的比值不宜過大(常在12左右);
在容易出現波紋處限制其平整度。
(6)局部強度加強
采用較大的板厚;加大支架緊固面尺寸,增多緊固數量,并盡量使力作用點接近腹板的上、下側面。
2.4車架的輕量化
由于車架較重,對于鋼板的消耗量相當大。因此,車架應按等強度的原則進行設計,以減輕汽車的自重和降低材料的消耗量。在保證強度的條件下,盡量減輕車架的質量。通常要求車架的質量應小于整車整備質量的10%。
本設計主要對車架縱梁進行簡化的彎曲強度計算,使車架縱梁具有足夠的強度,以此來確定車架的斷面尺寸。另外,從生產汽車的經濟性考慮的話,也應盡量減輕整車的質量。從生產工藝性考慮,橫縱梁采用簡便可靠的連接方式,不僅能降低工人的工作強度,還能增強車架的強度[12]。
2.5車架的參數設計
2.5.1車架長度確定
對于載重貨車而言,車架的長度一般可認為是整車的長度減去車輛最前端到車架最前端的距離,對于本車型而言,整車定義長度為 8445mm。車輛的最前端在保險杠上。保險杠最前端到車架前橫梁最前端的距離為 45mm,所以車架總長可確定為 8400mm,車架前懸為 1150mm,軸距為4700mm,車架后懸為 2550mm。
2.5.2車架寬度確定
車架的寬度是左、右縱梁腹板外側面之間的寬度。車架前部寬度的最小值取決于發(fā)動機的外廓寬度,其最大值受到前輪最大轉角的限制。車架后部寬度的最大值主要是根據車架外側的輪胎和鋼板彈簧片寬等尺寸確定。為了提高汽車的橫向穩(wěn)定性,希望增大車架的寬度。
通常,車架的寬度根據汽車總體布置的參數來確定,整車寬度不得超過2.5m,故往往很難同時滿足上述要求。為了解決總體布置與加寬車架的矛盾,車架的寬度設計可采取以下措施[13]:
(1)將車架做成前窄后寬
這種結構可以解決前輪轉向所需的空間與車架總寬之間的矛盾。此結構適用于輕型汽車、微型汽車和轎車。
(2)將車架做成前寬后窄
對于重型載貨汽車,其后軸的負荷大,輪胎的尺寸加大,后鋼板彈簧片寬增加,同時為了安裝外型尺寸大的發(fā)動機,常需減小前輪轉向角,以便使汽車的總寬在公路標準的2.5m內,因此車架不得不采用前寬后窄的型式。
(3) 將車架做成前后等寬
在整車布置允許的條件下,應該盡量采用前后等寬式車架,因為該結構車架的制造工藝簡單,不存在不等寬車架在皺紋區(qū)易產生應力集中的缺點,目前絕大多數中等載重量的汽車采用了前后等寬式車架。
根據本設計的要求,關于輕型載重貨車車架結構設計,其載重設為10t,簡化制造工藝,最好車架前后等寬。為了便于實行產品的三化,不少國家對車架的寬度制定了標準。我國汽車專業(yè)標準[18](汽132-59載重汽車車架寬度標準)規(guī)定“車架寬度標準為865?±5毫米”。根據汽車設計取車架寬860mm。
2.5.3車架縱梁結構設計
車架縱梁的斷面高度決定了貨物質心的高度,降低縱梁上翼面的離地高度不僅能降低駕駛室等裝置件的離地高度,也能降低車箱底板的離地高度,但降低車架縱梁斷面高度會嚴重的降低縱梁的抗彎能力,所以縱梁設計時這兩方面要綜合考慮。重型貨車通常多采用槽形斷面縱梁,這是因為縱梁主要承受彎曲載荷和便于裝配的緣故[14]。盡管槽形斷面的抗扭剛度遠遠不如閉口斷面 ,但由于在重型汽車上,許多裝置件(如汽油箱、儲氣筒、排氣管)的支架都是裝在縱梁上,若是將縱梁做成封閉斷面,則這些支架的安裝就會困難很多[16]。該載重貨車車架縱梁采用槽型梁,前后等高上下翼面平直的架構。統(tǒng)計對比同類車型,車架縱梁斷面高度初步判斷應在 300mm-320mm 之間,根據已有生產沖壓模具的條件,同時考慮輕量化問題縱梁梁斷面高度確定為 300mm[17],根據整車布置要求(特別是后簧平衡懸架支架限制,縱梁翼面寬 90mm)和車架抗彎、抗扭的需要,確定縱梁的翼面寬為 90mm;根據沖壓能力和使用條件分析,縱梁板料厚度確定為 8mm。縱梁的翼面橫截面如下圖2.5所示。
圖2.5 縱梁斷面尺寸
2.5.4車架橫梁結構設計
車架橫梁將左、右縱梁連接在一起,構成一個框架,使車架有足夠的抗彎剛度。汽車主要總成通過橫梁來支承。載貨汽車的橫梁一般有多根橫梁組成,其結構和用途不一樣[19]。
前橫梁
通常用來支承水箱。當發(fā)動機前支點安排在左右縱梁上時,可用較小槽型和Z型斷面橫梁。對于前部采用獨立懸架的轎車,為了改善汽車的視野,希望汽車頭部高度降低,固需要將水箱安裝得低些,可將前橫梁做成寬而下凹的形狀。當發(fā)動機前支點和水箱相距很近時,前橫梁常用來支承水箱和發(fā)動機前端,此時需采用斷面大的橫梁。中橫梁通常用來作傳動軸的中間支承。為了保證傳動軸有足夠的跳動空間,將其結構做成上拱形。在后鋼板彈簧前、后支架附近所受到的力或轉矩大,則要設置一根抗扭剛度大、連接寬度大的橫梁。后橫梁采用中橫梁形式。
本設計課題是關于載重貨車車架結構設計,所以采用開口斷面比較合適。本次設計一共采用大小共6根橫梁,各根橫梁的結構及用途如下:
第一根橫梁斷面形狀為槽型,用來支撐水箱,其中間設有多個圓形孔,目的是讓空氣可以流到發(fā)動機底部,也有助于發(fā)動機的散熱。
第二根橫梁為發(fā)動機托架,為防止其與前軸發(fā)生碰撞幾干涉,故將其安排放在發(fā)動機前端,其形狀就是近似元寶的元寶梁,此種形狀有較好的剛度。
第三根橫梁用作傳動軸的支承,其斷面形狀為槽形,為了保證傳動軸有足夠的跳動空間和安裝空間,將其結構做成上拱形。
第四、五根橫梁分別在后鋼板彈簧前、后支架附近,它們所受到的力或轉矩都很大。將其設計成K型。它們的斷面形狀也是采用槽形。
第六橫梁為后橫梁,其將左、右縱梁連接在一起,構成一個框架,使車架有足夠的抗彎剛度。其斷面形狀為槽形。
2.5.6橫梁縱梁連接方式
縱梁和橫梁的連接方式對車架的受力有很大的影響。大致可分有以下幾種:
(1) 橫梁和縱梁的腹板相連接
這種連接型式制造工藝簡單,連接剛度較差,但不會使縱梁出現大的應力,一般車架的中部橫梁采用此種連接方式。
(2) 橫梁同時和縱梁的腹板及任一翼緣(上或下)相連接
這種連接方式制造工藝不很復雜,連接剛度增強,故得到廣泛應用。但后鋼板彈簧托架上的力會通過縱梁傳給后鋼板彈簧的前橫梁,使其承受較大載荷。因此在設計鋼板彈簧托架時應盡可能減少懸架伸長度,使載荷作用點靠近縱梁彎曲中心。當偏心載荷較大時,可將該處縱梁做成局部閉口斷面;也可將橫梁穿過縱梁向外延伸,將載荷直接傳給橫梁。
(3) 橫梁同時和上、下翼緣相連接
這種連接形式具有剛性較好的加強角撐,可產生良好的斜支撐作用,使整個車架的剛度增加,且其翼緣外邊不致因受壓而產生翹曲。車架兩端的橫梁常采用這種形式和縱梁相連接。但此種連接方式制造復雜,當轉矩過大時,縱梁翼緣上會出現應力過大的現象,這是由于縱梁截面不能自由翹曲所致。
橫梁和縱梁的固定方法可分為鉚接、焊接和螺栓連接等方式。大多數車架用搭鐵板通過鉚釘連接。這種方法成本低,適合大批量生產,其剛度與鉚釘的數目及其分布有關。焊接能使其連接牢固,不致產生松動,能保證有大的剛度。但焊接容易變形并產生較大的內應力,故要求焊接質量要高,主要在小批量生產或修理時采用。
螺栓連接主要在某些為了適用于各種特殊使用條件的汽車車架上采用,以使裝在汽車車架上的某些部件易于拆卸或互換。但此種連接方式在長期使用時,容易松動,甚至發(fā)生嚴重事故。一般汽車車架橫梁與縱梁的固定不采用此種方法。
鉚接時緊固件的尺寸和數量要和橫梁大小相適應,鉚釘分布不要太近。當利用連接板的翻邊緊固時,應加大連接板的寬度和厚度,緊固孔應盡可能靠近翻邊處,以防連接損壞[20]。
本設計方案中,橫梁與縱梁的連接形式使用鉚接加螺栓連接,連接在腹板上。連接方式如圖2.6所示
圖 2.6 縱梁橫梁連接方式示意圖
3 車架的有限元靜力學分析
3.1車架幾何模型的建立
目前三維模型的繪圖軟件很多,常用的有UG、solidworks、Pro.E、CATRA等等。也可以在workbench中直接繪制三維模型圖。本次設計采用solidworks繪圖軟件根據第二章的設計數據繪制出車架的三維模型圖(圖3.1)。
圖3.1 車架三維模型圖
3.2車架有限元模型的建立
3.2.1將車架模型導入到workbench
在solidworks軟件中將車架的三維模型完成之后,將模型轉化為Workbench 軟件所識別的*.x-t格式,在SolidWorks 軟件中可以通過文件另存為實現。啟動Workbench 軟件后,通過import 選項導入車架的三維幾何模型*.x-t文件。導入到Workbench 軟件后生成的車架有限元模型圖。
3.2.2設置材料參數
本次設計整體結構采用B500L鋼[21],物理屬性如表3.1 所示
表3.1 B500L鋼材料力學性能
材料牌號
密度[kg/m3]
泊松比
彈性模量[MPa]
屈服強度[MPa]
抗拉極限強[MPa]
B500L鋼
7800
0.3
2.1E5
320
500
3.2.3有限元網格化分
有限元分析的基本思想就是把連續(xù)體劃分為離散的模型,劃分網格的目的是把連續(xù)體分解成可得到精確解的適當數量的單元。本論文所使用的車架幾何模型各零部件之間沒有相對運動,所以全部使用綁定接觸處理。
對于三維幾何來說,ANSYS Mesh 有Automatic(自動網格劃分)、Tetrahedrons(四面體網格劃分)、Hex Dominant(六面體主導網格劃分),本論文采用Tetrahedrons 中的Patch Conforming 法,它是可以快速地、自動地生成網格,并適合于復雜幾何體。四面體網格具有等向細化的特點,為捕捉一個方向的梯度,網格在三個方向細化,會導致網格數量迅速上升。選擇單元尺寸為20mm,這樣可以保證單元質量和連接孔周的單元數目適當。車架有限元劃分網格后如圖3.2 所示。節(jié)點數為407862個,單元網格數為202792 個。
圖3.2 車架的有限元網格化分
3.3車架的靜力學分析
要對車架進行靜力學分析,首先應該清楚了解的是車輛在行駛時車架所要承受的各種不同的力。如果車架在某方面的韌性不佳,就算有再好的懸掛系統(tǒng),也無法達到良好的操控表現。而車架在實際環(huán)境下要主要面對以下4種典型工況[22~24]。
(1)負載彎曲
從字面上就可以十分容易的理解這個壓力,部分汽車的非懸掛重量,是由車架承受的,通過輪軸傳到地面。而這個壓力,主要會集中在軸距的中心點。因此車架底部的縱梁和橫梁,一般都要求較強的剛度。
(2)非水平扭動
當前后對角車輪遇到道路上的不平而滾動,車架的梁柱便要承受這個縱向扭曲壓力,情況就好像要你將一塊塑料片扭曲成螺旋形一樣。 (3)橫向彎曲
所謂橫向彎曲,就是汽車在入彎時重量的慣性(即離心力)會使車身產生向彎外甩的傾向,而輪胎的抓著力會和路面形成反作用力,兩股相對的壓力將車架橫向扭曲。
(4)緊急制動
當汽車滿載在路面上勻速行駛突然遇到緊急狀況,緊急制動時,受慣性載荷的作用,車架彎曲變形。
3.3.1靜止負載彎曲
滿載彎曲工況是模擬汽車在滿載狀態(tài)下,四輪著地在良好路面上勻速行駛時車架對其所承受的重量的響應,滿載狀態(tài)也是載重貨車的一種極限工況,只要該工況下車架達到所要的設計標準,在正常工況下,該車架也必然會符合標準。
約束條件:對貨車主要部件質量做一個簡化處理如表3.2,然后集中加載在車架。
表3.2 車架載荷分布
總成
質量(kg)
駕駛室
800
發(fā)動機
500
變速箱
500
油箱(滿載)
250
其余總成簡化
2000
在建立車架有限元模型時,需將作用在車架上的外載荷簡化為等效載荷加到車架上。對于車身的自重及車架上的各總成,就將它們簡化為集中力直接作用在車架上。而載重汽車的載荷(承載重量)是通過貨箱傳給車架的,汽車貨箱主要由貨箱底板、貨箱橫梁和貨箱縱梁組成。貨箱的縱梁放在車架縱梁的上翼面上,兩者是通過若干個U形螺栓聯(lián)結在一起的,以往的車架有限元計算中,常常不考慮貨箱的剛度對車架剛度與強度的貢獻,而一概將貨箱上的載荷以集中力或均布力形式全部直接加到車架上,這種簡化的計算結果表明車架應力的計算值一般比實驗值大,特別在與貨箱相連的車架中后部應力計算值往往比實驗值大幾倍。事實上貨箱和車架之間的作用力是以集中力形式傳遞的,但并不是完全傳遞,而是與貨箱的剛度有關,若貨箱與車架是鋼一鋼結構連接(貨箱縱梁為鋼質材料),考慮到貨箱的剛度對車架強度的影響,則總載荷由車架和貨箱共同承擔,若貨箱與車架是木一一鋼結構連接,由于貨箱剛度小,因此只承擔了總載荷的弱,總載荷基本上是由車架承受。雖然實際上載重量以集中力的方式作用在車架上,但是作用的位置點具有不確定性,在本次試驗中還是按照均布力的方式均勻施加在車架上。車架與懸架連接的八個面施加固定位約束。然后在車架上施加載荷。發(fā)動機和變速箱按照集中力方式加載如圖3.4,駕駛室均勻分布在車架前端2200mm上,其余總成加總載重量10000kg按貨箱長度均勻分布在車架后端。如下圖3.3所示。
圖 3.3 貨物加載位置
圖 3.4 發(fā)動機變速箱集中加力位置
約束條件施加完以后,自動求解。
圖 3.5 滿載位移云圖
車架滿載靜止工況下的總變形如圖3.5 所示,由圖可以看出車架在滿載靜止工況下車架尾部的變形量最大,最大變形量為4.33mm,由于貨車車架的最大彎曲撓度通常小于10mm,所以該車架在靜態(tài)滿載工況下滿足性能要求。本車型由于車廂過長,所以車架后懸過長,模擬分析過程中載荷按照均勻分布,這才導致車架尾部變形最大。在實際使用中車廂尾端載重量不會過大,所以在實際使用中車架尾端變形量會更小。
由內部應力云圖3.6可以看出, 整個裝配體的等效應力都沒有超過屈服應力(320MPa)的部分,最大應力出現在后輪后支撐處,應力最大值136.47MPa,小于材料的屈服強度。因此,當車架滿載靜止時,滿足性能要求。
滿載時安全系數如圖3.7所示。
圖 3.6 滿載應力云圖
圖3.7 滿載安全系數
3.3.2靜止30%超載
與滿載相比,后車架貨箱位置多施加30%負載,求解之后。位移變化結果如下圖3.8:
圖 3.8 30%超載位移云圖
車架30%靜止工況下的總變形如圖3.10所示,由圖可以看出車架在滿載靜止工況下的最大變形量為5.7401mm,位于貨車尾端。由于貨車車架的最大彎曲撓度通常小于10mm,所以該車架在靜態(tài)30%超載工況下滿足性能要求。
由內部應力云圖3.9可以看出, 整個裝配體的等效應力都沒有超過屈服應力(320MPa)的部分,最大應力出現在后輪后支撐處,應力最大值202.61MPa,小于材料的屈服極限。因此,當車架30%超載時,滿足性能要求。
圖 3.9 30%超載應力云圖
經過分析對比,貨車在50%超載時,車架最大位移為6.6215mm如圖3.10所示。小于10mm。也能滿足性能要求。最大應力如下圖3.11所示為233.58Mpa<320Mpa,符合性能要求。
經過不同程度超載分析,該貨車車架性能滿足設計的載重要求,并且安全系數遠遠大于1,但考慮到在實際使用中,貨車不存在絕對的靜止情況,因此在靜止分析中安全系數遠大于1是非常有必要的。
圖3.10 50%超載位移變化云圖
圖3.11 50%超載內部應力云圖
3.3.3 非水平扭轉
扭轉工況主要是模擬汽車一側輪胎駛入凹坑或是遇到凸起障礙物時,車架發(fā)生最為嚴重扭曲,此時車架受到的應力及變形情況最為惡劣。這種情況一般發(fā)生在崎嶇不平的道路上,車速較低。給右前輪強制施加一個10mm的位移,其余三個輪按固定位移處理。算出車架的最大位移及應力云圖如下圖3.12和3.13所示:
圖3.12 車架扭曲變形位移云圖
圖3.13 車架扭曲變形應力云圖
圖3.14 車架扭曲變形局部應力云圖
可見,在扭曲變形工況下最大位移發(fā)生在車架右前部如圖3.14所示,最大位移為11.096mm。最大應力發(fā)生在懸架與車架連接處,最大應力為342.79Mpa,已經超過車架材料的屈服強度320Mpa,小于材料的抗拉極限強度500Mpa。過崎嶇路面車架的扭曲變形發(fā)生在瞬間且不會持續(xù),因此,該車架還是滿足性能要求的。
3.3.4橫向彎曲工況
汽車在行駛過程中,有時會遇到急轉彎的情況,因此離心力的作用,車架將受到側向載荷。按緊急右轉的極限狀態(tài)。轉彎狀況下車速按20km/h計算,轉彎半徑按10m計算。
根據側向加速度的計算公式
式 (3.1)
式中:a 汽車的側向加速度;
V 汽車的行駛速度;
R 轉彎半徑。
前輪施加固定約束,滿載工況下施加2.5m/側向加速度,求出其位移與應力云圖如下圖3.15和3.16所示。
可見,在緊急轉彎工況下,最大位移發(fā)生在車架末端,最大位移量為4.5354mm。最大應力發(fā)生在前懸架與元寶梁連接處,最大應力為154.15Mpa。小于車架材料的屈服強度。滿足車架的性能要求。
圖 3.15 橫向彎曲位移云圖
圖 3.16 橫向彎曲應力云圖
3.3.5緊急制動工況
當車輛遇到緊急情況進行制動時,車架會受到各部分的載荷作用和沿縱向產生的慣性力作用。本文研究的是滿載緊急制動工況,制動工況考慮前后車輪完全抱死的情況下,取附著系數φ=0.7,汽車制動時的最大減速度為0.7m/s。車架位移云圖和內部應力云圖如下圖3.17和3.18所示。
圖 3.17 緊急制動位移云圖
由云圖可以看出,車架在滿載靜止工況下的最大變形量為4.39mm,由于貨車車架的最大彎曲撓度通常小于10mm,所以該車架在靜態(tài)滿載工況下滿足性能要求。
等效應力都沒有超過屈服應力(493MPa)的部分,最大應力還是出現在左后輪后支撐處,應力最大值154.24MPa小于材料的屈服極限。因此,當車架滿載緊急制動時,滿足性能要求。
圖3.18 緊急制動應力云圖
3.4 基于靜力分析的車架輕量化
對汽車零部件的結構優(yōu)化可以通過使部件中空化、薄壁化、小型化和復合化達到目的,對于該輕型載貨貨車主要從減薄壁厚和添加減重孔來降低質量。
通過對車架四種典型工況靜態(tài)分析可以看出,貨車在除扭轉工況外,其余各種工況下,安全系數均大于1,就算在超載50%以后,車架的安全系數仍然大于1.因此此時可以考慮減薄壁厚來實現車架的輕量化,但是在扭轉工況下,當給右前輪強制施加一個向上的位移時,車架的最高內部應力超過材料的屈服強度,但我們可以看出超出屈服強度的部分只有右前輪車架與懸架的連接處,如下圖3.19所示;
圖 3.19 車架扭轉變形局部應力云圖
因此我們可以通過加強懸架與車架的連接,同時用強度更高強度的材料來替換懸架與車架連接處的材料,達到更安全的目的。同時還可以通過增大橫梁上的圓孔直徑來減少材料用量,已達到輕量化的目的。從經濟方面考慮,也可以換用價格更低廉的材料。
4 車架的模態(tài)分析
4.1車架模態(tài)分析的基本理論
在汽車行駛時,作用在汽車各部件上的載荷都是動載荷。若所受動載荷較小時,只需進行靜態(tài)分析即可。若汽車行駛在凹凸不平的道路上,使得在它上面行駛的車輛產生垂直方向的位移變動,道路表面的凹凸不平是隨機的,它對車輛產生隨機激勵。如果這種隨機激勵引起的振動過大的話,將使得乘員感到不舒服和不適應,對車架造成強度破壞或產生不允許的大變形[25]。因此我們有必要研究汽車結構振動的固有頻率及其相應的振型。模態(tài)是振動系統(tǒng)特性的一種表征,它實為構成各種工程結構復雜振動的那些最簡單或最基本的振動形態(tài)。通過模態(tài)分析可以得到結構的固有頻率和主要振型,為振動系統(tǒng)動態(tài)設計及故障診斷提供依據,同時,它也是其它更詳細動力學分析(如諧響分析、瞬態(tài)動力學分析和譜分析)的基礎[26]。
車輛是一個復雜的機械系統(tǒng),從動力學的觀點來看,車輛本身就是一個具有質量、彈性和阻尼的震動系統(tǒng)。由于車輛內部各總成、零部件的固有頻率不同,減震方式不同,在行駛中常因路面不平,車速和運動方向的變化,車輪、發(fā)動機和傳動系統(tǒng)的不平衡,以及齒輪的沖擊等各種外部和內部的激振作用而產生的整車和局部的振動,這種振動使車輛的動力性得不到充分的發(fā)揮,經濟型變壞。同時還影響車輛的操縱穩(wěn)定性和平順性,甚至損壞車輛的零部件和運載的貨物,縮短車輛用壽命[27]。
有限元法為結構的動態(tài)分析提供了一種有效的工具,應用有限元進行車輛結構的動態(tài)分析??梢缘玫杰囕v的各階固有頻率及振型,這一方面可以了解車輛結構的固有動力學特征,另一方面又為進一步進行車輛結構的動態(tài)響應分析奠定基礎。通過車輛構的諧響應分析,可以得到車輛結構在發(fā)動機、傳動系統(tǒng)及輪胎的不平衡所造成的簡諧激振力作用下的動力學響應。
一個N 自由度線性系統(tǒng),其運動微分方程為
式(4.1)
式中:M——質量矩陣;
K——剛度矩陣;
X——位移向量;
F(t)——作用力向量;
t——時間。
由于結構的阻尼問題比較復雜,并且大量實驗結果表明,大多數結構的阻尼比都非常小,對系統(tǒng)的固有頻率和振興的計算結果影響都比較小,可以忽略不計,在模態(tài)分析時,令=0。
當F(t)=0 時,忽略阻尼C 影響,方程變?yōu)?
式(4.2)
自由振動時,結構上各點作簡諧振動,各節(jié)點位移
式(4.3)
由式(4.2)、(4.3)得
式(4.4)
求出特征值和特征值。
求得系統(tǒng)各階固有頻率即模態(tài)頻率,固有振型即模態(tài)振型。
4.2車架有限元模態(tài)分析結果
在進行車架結構設計時,要保證車架的低階頻率介于發(fā)動機怠速運轉頻率和非簧載結構的固有頻率之間,以防止整體共振的發(fā)生。車架彈性模態(tài)頻率也應避開發(fā)動機經常工作的頻率范圍。車架激勵一般來源于路面和發(fā)動機。路面的激勵頻率多在20Hz以下,該車發(fā)動機的怠速為900r/min相應發(fā)動機的爆發(fā)頻率為30Hz,發(fā)動機正常工作時經常使用發(fā)動機轉速為1200~1400r/min相應的發(fā)動機爆發(fā)頻率為40Hz.模態(tài)分析主要用來獲得結構的固有頻率和振型,而結構的固有頻率和振型對于承受動態(tài)載荷的結構是十分重要的參數??梢宰鳛閯恿W分析的基礎。根據模態(tài)分析理論,通常大型的工程結構由于低階振動對結構影響最大,因此,此次結構的模態(tài)分析只計算0~100Hz頻率范圍內的固有頻率和振型即可。對車架有限元模型進行模態(tài)求解,本次提取了前6 階頻率。各頻率值如表4.1,五階以上頻率已經超過100Hz,所以六階頻率以上不再考慮。
表4.1 車架前六階模態(tài)分析結果
階數
頻率/HZ
最大變形/mm
1
35.002
3.4392
2
39.591
2.9652
3
41.530
4.0111
4
55.04
4.6436
5
102.58
3.1795
6
103.14
4.4512
圖4.1 車架的第一階振型
第一階模態(tài)分析如圖4.1頻率為35.002Hz,振型為尾部側向擺動,車架尾部變形最大。最大變形量為3.44mm。
4.2 車架的第二階振型
第二階模態(tài)分析如圖4.2頻率為39.591Hz,振型為車架中間側向彎曲,中間處變形最大。最大變形量為2.9707mm。
圖4.3 車架的第三階振型
第三階模態(tài)分析如圖4.3頻率為41.53Hz,振型為車架尾部上下俯仰,最大變形出現在車架最尾端。最大變形量為4.0201mm。
圖 4.4 車架的第四階振型
第四階模態(tài)分析如圖4.4頻率為55.54Hz,振型為車架尾端扭轉變形。最尾端扭轉變形最嚴重。最大變形量為4.7074mm。
圖 4.5 車架的第五階振型
第五階模態(tài)分析如圖4.5頻率為102.58Hz,振型為靠近車架尾端的地方發(fā)生側向彎曲,最大變形處發(fā)生在車架后橋與尾端中間處,最大變形量為2.2083mm。
圖 4.6 車架的第六階振型
第六階模態(tài)分析如圖4.6頻率為103.14Hz,振型為發(fā)動機支架處發(fā)生扭曲變形,最大變形出現在發(fā)動機支架下端,最大變形量為4.4781mm。
4.3車架外部激勵分析
4.3.1車架動態(tài)特性要求
為防止車架工作過程中發(fā)生共振,車架的固有頻率應滿足以下要求:
(1)低階頻率應低于或高于發(fā)動機怠速運轉頻率,以避免在怠速下發(fā)生整車共振。
(2)彈性模態(tài)頻率應盡量避開發(fā)動機經常工作的頻率范圍。
(3)固有頻率,應避開路面不平度的激勵頻率。
(4)固有頻率之間有一定的距離,避免頻率耦合。
4.3.